The oil and gas industries are always looking for ways to improve, to make things more efficient and reliable. One of those innovations is the use of liquid ring vacuum pumps. These have become a staple in the industry due to their ruggedness, efficiency and versatility.
What are Liquid Ring Vacuum Pumps?
Liquid ring vacuum pumps, also known as liquid vacuum pumps, are mechanical devices that use a liquid, usually water or oil, to create a vacuum. This is used in the oil and gas industry for various applications such as gas compression, vapour recovery and air evacuation.
Liquid ring vacuum pumps work by using the liquid to form a rotating ring inside the pump body which seals and compresses the gases. This unique operation has several benefits, such as ability to handle wet and contaminated gases, a big plus in the harsh environment of oil and gas operations. The liquid ring also acts as a coolant which helps to keep the pump temperature down and prevent overheating so the pump can run continuously and reliably.
How does a Liquid Ring Vacuum Pump Work?
Understanding the liquid ring vacuum pump working principle is key to understanding its benefits and applications. The pump has a cylindrical body with an eccentrically mounted rotor inside.
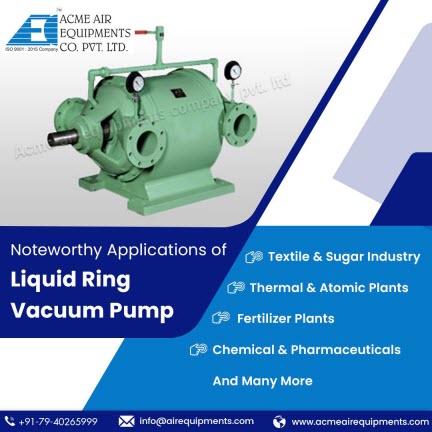
As the rotor spins the liquid (forming the ring) is forced against the body walls due to centrifugal force. This creates a series of sealed chambers between the rotor blades and the liquid ring.
These chambers expand and contract as the rotor turns, draws in gas through an inlet port, compresses it and then discharges it through an outlet port. This continuous process gives a smooth and steady flow of vacuum and compressed gas, making liquid ring vacuum pumps very efficient and reliable. This also means the pump can handle a mixture of gases and liquids without damage, making it suitable for applications where the gases are saturated with liquids or have impurities.
Key Components of Liquid Ring Vacuum Pumps
The primary liquid ring vacuum pump parts include:
- Casing: The outer shell that houses all internal components, designed to withstand the pressures and corrosive environments often encountered in the oil and gas industries.
- Rotor: The rotating part that creates the liquid ring and the compression chambers. Made from materials that can endure high rotational speeds and abrasive conditions.
- Liquid Sealant: Typically water or oil, used to form the liquid ring. The choice of liquid depends on the application and the type of gases being handled.
- Shaft: Connects the rotor to the motor, enabling the rotation. Precision-engineered to ensure minimal vibration and efficient power transmission.
- Inlet and Outlet Ports: Allow gases to enter and exit the pump. These ports are designed to facilitate smooth gas flow and prevent backflow, ensuring efficient operation.
Understanding these components is essential for maintaining and troubleshooting the pump. Regular inspection and maintenance of these parts can prevent common issues and prolong the life of the pump.
Types of Liquid Ring Vacuum Pumps
There are different types of liquid ring vacuum pumps tailored for various applications:
Single Stage Liquid Ring Vacuum Pumps
These pumps are ideal for applications requiring moderate vacuum levels. They are simpler in design and cost-effective, making them suitable for general industrial use. Single stage pumps have one compression stage, which is sufficient for many standard operations, such as vacuum filtration and evacuation of air from condensers.
Two Stage Liquid Ring Vacuum Pumps
For applications requiring higher vacuum levels, two stage liquid ring vacuum pumps are preferred. These pumps have two sets of compression chambers, allowing them to achieve deeper vacuums and handle more demanding applications in the oil and gas industries. Two-stage pumps are often used in processes that require a higher degree of gas purity or lower ultimate vacuum levels, such as in the production of certain chemicals and in vacuum distillation processes.
Applications of Liquid Ring Vacuum Pumps in Oil and Gas Industries
Liquid ring vacuum pumps are versatile and find numerous applications in the oil and gas sectors:
Gas Compression
In natural gas processing, these pumps are used for compressing gases. Their ability to handle wet gases without damage makes them ideal for this application. The gas compression process often involves handling gases that are saturated with liquids, and liquid ring pumps can efficiently manage these conditions without performance degradation.
Vapour Recovery
They are also used in vapour recovery units (VRUs) to capture and compress hydrocarbon vapours. This not only reduces emissions but also recovers valuable hydrocarbons. Vapour recovery is a critical process in reducing environmental impact and improving the overall efficiency of oil and gas operations. The ability of liquid ring pumps to operate continuously and reliably makes them well-suited for this application.
Air Evacuation
During the drilling and production stages, air evacuation is crucial to prevent explosions and maintain safety. Liquid ring vacuum pumps efficiently evacuate air and other gases from wells and pipelines. The robust construction of these pumps allows them to perform effectively in the harsh conditions often found in drilling environments, ensuring safety and operational efficiency.
Degassing
In refineries, liquid ring pumps are used to remove gases from liquids, ensuring the purity and quality of the final product. Degassing is a vital step in processes such as vacuum distillation and solvent recovery, where the presence of gases can affect the efficiency and outcome of the operation. Liquid ring pumps provide a reliable solution for maintaining product quality and process efficiency.
Advantages of Liquid Ring Vacuum Pumps
Reliability and Durability
One of the main reasons for the widespread use of liquid ring vacuum pumps in the oil and gas industries is their reliability. The simple yet robust design ensures long operational life with minimal maintenance. These pumps are built to withstand the challenging conditions of the oil and gas sector, including exposure to corrosive gases and high operational pressures.
Handling of Wet and Saturated Gases
Unlike other types of pumps, liquid ring vacuum pumps can handle wet and saturated gases without risk of damage. This makes them particularly suited for the humid and often harsh environments of the oil and gas industries. The liquid ring not only seals and compresses the gases but also cools the pump, preventing overheating and ensuring continuous operation.
Smooth Operation
The continuous and smooth operation of these pumps reduces wear and tear on system components, leading to lower maintenance costs and less downtime. The absence of metal-to-metal contact within the pump means that there is minimal mechanical wear, contributing to the longevity and reliability of the pump.
Versatility
Liquid ring vacuum pumps can be adapted to a wide range of applications by simply changing the sealant liquid. This versatility is highly valued in the dynamic oil and gas industries, where operational conditions can vary significantly. Whether it’s water, oil, or another compatible liquid, the choice of sealant can be tailored to meet the specific needs of the application.
Challenges and Considerations
While liquid ring vacuum pumps offer numerous benefits, there are some challenges and considerations to keep in mind:
Liquid Management
Proper management of the sealant liquid is crucial. Inadequate liquid levels or contaminated liquid can affect the pump’s performance and longevity. Regular monitoring and maintenance of the liquid levels and quality are essential to ensure optimal pump operation. Additionally, the choice of liquid should be compatible with the gases being handled to prevent chemical reactions and corrosion.
Energy Consumption
These pumps can be energy-intensive, especially in applications requiring continuous operation. Therefore, it is important to balance the energy costs with the operational benefits they provide. Energy-efficient models and optimised operational strategies can help mitigate the energy consumption concerns associated with liquid ring vacuum pumps.
Installation and Maintenance
Professional installation and regular maintenance are essential to ensure optimal performance and avoid costly breakdowns. Working with experienced liquid ring vacuum pumps manufacturers can help mitigate these challenges. Proper installation ensures that the pump operates within its designed parameters, while regular maintenance helps identify and address potential issues before they lead to significant problems.
Selecting the Right Liquid Ring Vacuum Pump
Choosing the right pump involves considering several factors:
- Application Requirements: Understand the specific needs of your application, such as the required vacuum level and gas composition. Different applications have different demands, and selecting a pump that meets these requirements is crucial for achieving optimal performance.
- Pump Size and Capacity: Ensure the pump is appropriately sized for your system to avoid inefficiencies and potential damage. An undersized pump may not provide the necessary vacuum, while an oversized pump can lead to unnecessary energy consumption and higher operational costs.
- Material Compatibility: The materials of construction should be compatible with the gases and liquids being handled to prevent corrosion and wear. Selecting the right materials ensures the longevity and reliability of the pump, especially in harsh chemical environments.
- Manufacturer Support: Partnering with reputable liquid ring vacuum pump manufacturers ensures you get quality products and reliable support. Manufacturers with a proven track record in the oil and gas industries can provide valuable insights and assistance in selecting, installing, and maintaining the pump.
Liquid Ring Vacuum Pump Price and Cost Considerations
The liquid ring vacuum pump price can vary based on several factors including size, capacity, material, and manufacturer. While initial costs can be significant, it is important to consider the long-term benefits and cost savings from reduced maintenance and increased efficiency.
Investment in Quality
Investing in high-quality pumps from reputable manufacturers often translates to better performance, reliability, and longer service life. This can result in significant savings over the operational lifespan of the pump. High-quality pumps are designed to withstand the demanding conditions of the oil and gas industries, ensuring that they continue to operate efficiently and reliably over many years.
Conclusion
Liquid ring vacuum pumps play a critical role in enhancing the efficiency and safety of operations in the oil and gas industries. Their unique ability to handle wet and saturated gases, coupled with their reliability and versatility, makes them an invaluable asset. By understanding their working principles, selecting the right type, and ensuring proper maintenance, these pumps can provide significant operational benefits.
FAQ on Implementing Liquid Ring Vacuum Pumps in Oil and Gas Industries
Liquid ring vacuum pumps offer several distinct benefits to the oil and gas industry. They are highly reliable and can operate under harsh conditions, making them ideal for this sector. Their ability to handle gases containing liquids and impurities without damage is particularly valuable. Additionally, they provide efficient and continuous operation, which is crucial for maintaining productivity in oil and gas processes.
Liquid ring vacuum pumps create a vacuum through a unique method involving a rotating impeller and a sealing liquid. The impeller is offset within the pump casing, and as it spins, it forces the liquid to form a ring inside the casing. This ring of liquid creates sealed chambers that expand and contract, drawing in gas, compressing it, and then expelling it. This process generates a smooth and consistent vacuum.
Several components are essential for the proper functioning of liquid ring vacuum pumps. These include the pump casing, which houses the internal parts; the rotor, which creates the liquid ring; the liquid sealant, which forms the ring and aids in compression; the shaft, which connects the rotor to the motor; and the inlet and outlet ports, which manage the flow of gases into and out of the pump. Each of these components must be well-maintained to ensure efficient operation.
Liquid ring vacuum pumps are used in various applications within the oil and gas industry. These include gas compression in natural gas processing, vapour recovery in hydrocarbon capture, air evacuation during drilling operations, and degassing in refining processes. Their ability to handle wet and contaminated gases makes them suitable for these diverse applications.
When choosing a liquid ring vacuum pump, several factors need to be considered. These include the specific requirements of the application, such as the necessary vacuum level and the type of gases involved. Additionally, the pump’s size and capacity should match the system’s needs, and the materials used in the pump should be compatible with the gases and liquids it will handle. It is also important to consider the reputation and support provided by the manufacturer.
Regular maintenance is crucial for the optimal performance of liquid ring vacuum pumps. Maintenance tasks include monitoring the levels and quality of the liquid sealant, inspecting and cleaning the rotor and other components, and ensuring that the inlet and outlet ports are free from blockages. Regular upkeep helps prevent issues that could lead to reduced efficiency or breakdowns, thereby extending the pump’s operational life and maintaining its reliability.
Using liquid ring vacuum pumps in oil and gas operations can present certain challenges. Proper management of the sealant liquid is essential, as inadequate levels or contamination can impair performance. These pumps can also consume significant amounts of energy, so it’s important to consider energy efficiency. Additionally, professional installation and ongoing maintenance are necessary to prevent operational problems and ensure long-term reliability. Working with experienced manufacturers can help mitigate these challenges.
Positive Displacement Blower | Tri Lobe Blowers | Gas Boosters | Cement Feeding System | Dust Collector System | Catalyst Loading / Unloading Systems | Pneumatic Conveyor | Mechanical Vacuum Boosters | Vacuum Pumps | Liquid Ring Vacuum Pump | Water Ring Vacuum Pump | Two Stage Vacuum Pump | Oil Sealed Vacuum Pump | Big Bag Unloading System | Turbo Blower
© 2024 Acme Air Equipments | All Rights Reserved