Liquid Ring Vacuum Pumps are versatile, efficient and widely used in industries such as chemical processing, pharmaceuticals and power generation. Their unique design and reliable operation make them an essential choice for applications requiring efficient vacuum solutions. To truly understand how these pumps work, it is crucial to explore their key components: the casing, impeller and sealing liquid system.
This article provides a comprehensive overview of these components explains their roles in a liquid ring vacuum pump and highlights why Acme Air Equipments is a trusted manufacturer of high-quality vacuum solutions?
What Is a Liquid Ring Vacuum Pump?
A liquid ring vacuum pump is a rotary displacement pump that uses a liquid ring as a sealing medium to compress and move gases. These pumps are known for their durability, low maintenance and ability to handle wet, dry or contaminated gases.
Key Applications
- Chemical Processing: Vapor recovery, distillation and degassing.
- Pharmaceuticals: Vacuum drying and solvent recovery.
- Food Processing: Vacuum packaging and freeze-drying.
- Power Plants: Condenser evacuation and air extraction.
Understanding the Components of a Liquid Ring Vacuum Pump
A liquid ring vacuum pump consists of three primary components, each playing a crucial role in its operation.
Casing: The Structural Backbone
The casing is the outer shell of the liquid ring vacuum pump. It houses the internal components, including the impeller and the sealing liquid and ensures the pump’s structural integrity.
Features of the Casing
- Material Durability: Typically made from stainless steel, cast iron or other corrosion-resistant materials to withstand harsh environments.
- Precision Engineering: Designed to ensure minimal air leakage and optimal performance.
- Cooling Jackets: Some casing features cooling systems to manage heat generated during operation.
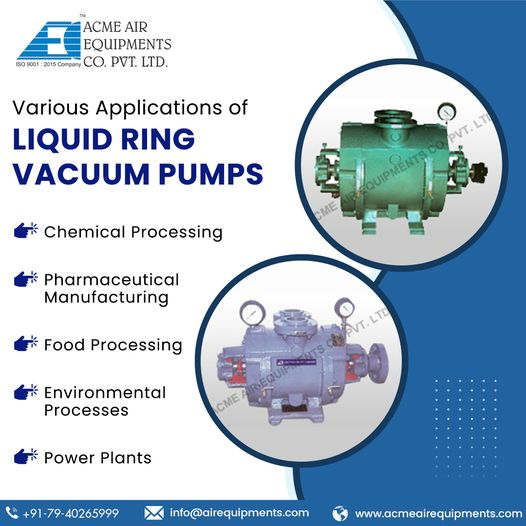
Role of the Casing
- Maintains the pump’s internal vacuum by preventing external air.
- Protects internal components from damage caused by environmental factors or operational stresses.
- Provides a secure enclosure for the impeller and sealing liquid.
Why It Matters?
A well-designed casing can significantly improve the pump’s efficiency and longevity, reducing maintenance costs and ensuring reliable performance.
Impeller: The Heart of the Pump
The impeller is the rotating component that creates the liquid ring and drives the pump’s operation. Its design and material are critical for the pump’s efficiency and ability to handle specific applications.
Design Features
- Blades or Vanes: These are precisely angled to optimize the movement of the sealing liquid.
- High-Strength Materials: Impellers are often made from materials such as stainless steel or bronze to withstand wear and corrosion.
- Balanced Construction: Ensures smooth operation and reduces vibration.
Role of the Impeller
- Creates centrifugal force that forms the liquid ring, essential for sealing and compressing gases.
- Transfers energy to the sealing liquid, facilitating efficient gas compression.
- Maintains continuous rotation to ensure consistent vacuum levels.
Why It Matters?
The efficiency of the impeller directly affects the pump’s performance. Properly designed impellers may increase energy efficiency and extend the lifespan of the pump.
Sealing Liquid System: The Essential Medium
The sealing liquid is the working fluid that forms the liquid ring within the pump. It plays a dual role in sealing and compressing gases while also cooling the system during operation.
Features of the Sealing Liquid System
- Water or Other Liquids: Commonly used sealing liquids include water, oil or other specialized fluids, depending on the application.
- Liquid Flow Control: Ensures the right amount of liquid is supplied for optimal performance.
- Heat Dissipation: Acts as a cooling agent, preventing overheating during prolonged use.
Role of the Sealing Liquid
- Forms a rotating liquid ring that seals the gaps between the impeller blades and the casing.
- Compresses gases as they pass through the pump.
- Dissipates heat generated by compression and friction.
Why It Matters?
The quality and management of the sealing liquid directly influence the pump’s efficiency and the quality of the vacuum produced.
How Liquid Ring Vacuum Pumps Work?
Liquid ring vacuum pumps operate by using the centrifugal force generated by the impeller to create a liquid ring inside the casing. Here’s an explanation:
- Liquid Introduction: Sealing liquid is introduced into the casing.
- Impeller Rotation: The rotating impeller creates centrifugal force, forming a liquid ring along the casing walls.
- Gas Compression: Gas enters the pump through an inlet port and is compressed as it moves between the liquid ring and impeller blades.
- Gas Discharge: Compressed gas is expelled through an outlet port, completing the cycle.
Advantages of Liquid Ring Vacuum Pumps
Handles Contaminated Gases
Liquid ring pumps can handle wet, dirty or corrosive gases, making them suitable for challenging environments.
Durable and Reliable
Their robust construction verifies long-lasting performance with minimal maintenance.
Oil-Free Operation
Unlike oil-sealed pumps, liquid ring pumps do not require oil, reducing contamination risks.
Quiet Operation
Designed to operate with low noise and vibration levels.
Versatile Applications
can be used in a wide range of industries due to their ability to handle diverse materials and conditions.
Why Choose Acme Air Equipments for Liquid Ring Vacuum Pumps?
As one of the leading liquid ring vacuum pump manufacturers, Acme Air Equipments has built a reputation for delivering high-quality, reliable and efficient vacuum solutions.
Advanced Engineering
- Acme’s pumps feature precision-engineered components for optimal performance and durability.
Customization Options
- Offers tailored solutions to meet the specific needs of different industries.
High-Quality Materials
- Uses corrosion-resistant materials to ensure long-lasting reliability.
Comprehensive Support
- Provides support, from installation to maintenance, ensuring seamless operation.
Focus on Sustainability
- Designs energy-efficient pumps that reduce operational costs and environmental impact.
Applications of Liquid Ring Vacuum Pumps
Chemical and Petrochemical Industries
- Applications: Distillation, solvent recovery and gas handling.
- Benefits: Safe handling of corrosive gases and chemicals.
Pharmaceuticals
- Applications: Vacuum drying, distillation and sterilization.
- Benefits: Maintains clean and contamination-free environments.
Power Plants
- Applications: Condenser evacuation and air extraction.
- Benefits: Enhances power generation efficiency.
Food Processing
- Applications: Freeze-drying, vacuum packaging and dehydration.
- Benefits: Preserves product quality and extends shelf life.
FAQs About Liquid Ring Vacuum Pumps
Yes, liquid ring pumps are designed to handle corrosive and contaminated gases with appropriate material selection.
The choice of sealing liquid depends on the application. Water is common, but specialized liquids may be used for specific processes.
The impeller’s design and material significantly influence energy efficiency and performance.
Conclusion
The effectiveness of a liquid ring vacuum pump lies in its well-designed components: the casing, impeller and sealing liquid system. Each element works harmoniously to provide efficient, reliable and versatile vacuum solutions for a wide range of industries.
With Acme Air Equipments, you’re not just investing in a pump- you’re investing in a high-performance, durable solution that can elevate your operations. Take the next step today and experience the difference.