In many vacuum applications, conventional mechanical vacuum pumps fall short of delivering the required capacity and hence their use in such applications becomes uneconomic and in some cases impossible. Pumping requirements in such applications exceed the capabilities of conventional mechanical vacuum pump.
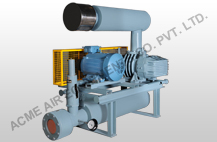
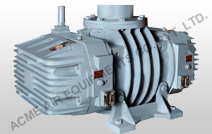

It is advisable to install mechanical vacuum booster, which acts as an auxiliary unit to conventional vacuum pump, for applications where higher vacuum is required along with reduced ultimate pressure. This mechanical vacuum booster will improve the overall performance of the conventional vacuum pump.
Mechanical vacuum boosters have been used as an integral part of many vacuum pumping systems for several decades. Mechanical vacuum boosters help in shorter evacuation time, increase in pumping capacity, high vacuum, reduction in size of primary pump and achieving pressure range which the primary pump cannot obtain.
Acme Air Equipments Co. Pvt. Ltd., an ISO 9001-2008 quality certified company, manufactures mechanical vacuum boosters and booster systems of highest quality standards in the state-of-art manufacturing setup along with comprehensive industrial solutions. This covers a wide spectrum of vacuum between 10 and 10-3 mbar.
Design and construction of mechanical vacuum booster involves two counter rotating impellers with a special contour. These vacuum booster pumps rotate with a sharp and a finite clearance in between them without any physical contact. Complete mechanical vacuum booster system is designed with vacuum booster at the core and connected with other equipments like primary pump, condensers, filters, valves, drives and instrumentation to function in desired mode. Integration of system is done by utilizing two stage liquid ring pump / oil sealed vacuum pump / rotary dry vacuum pump / reciprocating pump / steam or water jet ejectors as primary pump.
Types of Mechanical Vacuum Boosters
Understanding the types of mechanical vacuum boosters helps in selecting the right system for specific applications:
- Single-Stage Vacuum Booster Pumps: These are ideal for applications requiring moderate vacuum levels and are used in combination with rotary or liquid ring pumps.
- Two-Stage Vacuum Booster Pumps: These systems provide higher vacuum ranges and are typically paired with oil-sealed or dry screw vacuum pumps.
- High-Performance Vacuum Boosters: Designed for high-capacity vacuum systems, these are equipped with advanced cooling mechanisms to handle intense workloads.
Advancements in Mechanical Vacuum Boosters
Modern mechanical vacuum boosters are evolving to meet the increasing demands of industries requiring ultra-high vacuum performance. With advancements in materials, design, and technology, these systems now offer:
- Enhanced Durability: Use of corrosion-resistant alloys for impellers and casings ensures longer operational life, even in harsh environments.
- Energy Efficiency: Innovative designs in booster vacuum pumps reduce power consumption while maintaining high vacuum performance.
- Compact Designs: Space-saving configurations make them ideal for facilities with limited installation areas.
- Digital Monitoring and Control: Integration of sensors and IoT technologies enables real-time monitoring of performance metrics such as vacuum pressure, pump temperature, and impeller speed, ensuring optimal system efficiency.
Common applications of mechanical vacuum booster includes vacuum drying applications, vacuum distillation processes, solvent recovery, vacuum flash cooling, vacuum heat treatment, de-gassing, coating, refining of industrial oil, vacuum impregnation, semi conductor processing, separation of fluids, space simulation, vacuum freeze drying.
Emerging Applications of Mechanical Vacuum Boosters
The use of mechanical vacuum boosters is expanding into new fields due to their versatility and efficiency:
- Pharmaceutical Industry: These boosters are essential for vacuum distillation, solvent recovery, and drying processes, ensuring product purity and quality.
- Environmental Engineering: Used in wastewater treatment plants for degassing and air separation processes.
- Space Exploration: Critical in space simulation chambers for testing spacecraft components under vacuum conditions.
- Renewable Energy: Vacuum boosters play a role in manufacturing solar panels and other renewable energy components requiring precision coating.
Key Advantages of Using Vacuum Booster Pumps
- Faster Processing Times: By increasing the effective pumping speed, mechanical vacuum boosters significantly reduce evacuation times in critical applications.
- Reduction in Primary Pump Load: Mechanical vacuum boosters reduce the workload on the primary vacuum pump, improving its lifespan and energy efficiency.
- Improved Process Reliability: These systems ensure stable vacuum levels, which is crucial for processes like vacuum coating, freeze-drying, and heat treatment.
- Wide Range of Operating Pressures: Vacuum booster pumps can handle a wide spectrum of vacuum requirements, making them versatile for use across industries.
Maintenance Tips for Long-Term Performance
Regular maintenance is essential to ensure the efficient functioning of mechanical vacuum boosters:
- Routine Inspection: Periodically check for wear and tear on impellers, seals, and bearings.
- Lubrication: Maintain proper lubrication levels to reduce friction and prevent overheating.
- Filter Cleaning: Keep the filters clean to prevent blockages and maintain consistent airflow.
- Calibration of Sensors: For systems equipped with digital monitoring, ensure sensors and instrumentation are calibrated regularly.
- Replacement of Worn Components: Promptly replace any worn or damaged components to avoid system breakdowns.
For more details on mechanical vacuum booster, feel free to reach us at www.acmeairequipmemnts.com