Table of Contents
Pneumatic conveying systems are essential for efficiently transporting bulk materials, powders, granules, and other solid substances across various industries. As one of the largest and most industrialized economies in Latin America, Brazil plays a critical role in the demand for these systems. Industries such as agriculture, food processing, chemicals, and mining have driven the growth in the use of pneumatic conveying systems to enhance efficiency, minimize labor costs, and maintain safety standards. This article explores the demand and supply of pneumatic conveying systems in Brazil, focusing on key cities and industries.
Key Industries Driving Pneumatic Conveying System Demand in Brazil
1. Agriculture Brazil is one of the world’s largest agricultural producers, with a focus on commodities such as soybeans, sugar, coffee, and grains. Pneumatic conveying systems play a significant role in agriculture, particularly in the transportation of grains and fertilizers. The efficient movement of agricultural products through large processing facilities is crucial for maintaining the supply chain, reducing manual labor, and minimizing material loss.
Reason for Demand: The need for automation and the rising demand for crop production in Brazil have led to an increasing demand for pneumatic conveying systems. These systems enable the swift and efficient transportation of grains and fertilizers across farms, silos, and processing plants.
2. Food Processing Brazil’s food processing industry is one of the largest in the world, focusing on the production of packaged foods, beverages, and ingredients. With an increasing demand for bulk materials such as flour, sugar, spices, and additives, pneumatic conveying systems are becoming increasingly essential in the industry.
Reason for Demand: The food processing sector requires efficient transportation solutions that maintain hygiene standards and reduce contamination risks. Pneumatic conveying systems, with their closed-loop design, are ideal for these applications, enabling safe, hygienic, and efficient movement of raw materials from storage to processing units.
3. Chemical Processing Brazil’s chemical industry is another significant driver for pneumatic conveying systems. The transportation of various chemicals, powders, plastics, and other materials within chemical plants requires highly efficient and safe systems.
Reason for Demand: Chemical processing plants often handle hazardous and sensitive materials. Pneumatic conveying systems provide a safe method of transport, minimizing exposure to dangerous chemicals and ensuring the integrity of the materials being conveyed.
4. Mining Brazil is one of the largest producers of minerals, including iron ore, bauxite, and gold. Pneumatic conveying systems are widely used in mining operations to transport minerals and other bulk materials, especially in remote locations or over long distances where conventional conveyor systems may not be feasible.
Reason for Demand: The rugged terrain and long distances involved in transporting minerals in Brazil require specialized conveying solutions. Pneumatic conveying systems offer the flexibility to move materials across various landscapes with minimal environmental impact and maintenance.
City-wise Demand for Pneumatic Conveying Systems in Brazil
Pneumatic conveying systems are in demand across several key cities in Brazil, where industries like agriculture, food processing, chemicals, and mining are concentrated. These cities play a significant role in the country’s overall industrial output, driving demand for these systems.
1. Pneumatic Conveying Systems in São Paulo
- Key Industries: Agriculture, food processing, chemicals.
- Reason for Demand: São Paulo is the industrial heart of Brazil, with a thriving food processing sector and a strong presence of agricultural trade. The city’s food production plants and warehouses require efficient methods for transporting raw materials and finished products. Additionally, the chemical industry in São Paulo demands pneumatic conveying systems for handling sensitive and hazardous materials.
2. Pneumatic Conveying Systems in Rio de Janeiro
- Key Industries: Mining, chemicals, food processing.
- Reason for Demand: With its proximity to key mining regions in Brazil, Rio de Janeiro has seen an increase in demand for pneumatic conveying systems in the mining and chemical sectors. The city is also home to a robust food processing industry, which drives demand for systems that can safely and efficiently handle bulk food ingredients.
3. Pneumatic Conveying Systems in Belo Horizonte
- Key Industries: Mining, food processing.
- Reason for Demand: Belo Horizonte is an important city in Brazil’s mining sector, especially for iron ore. The demand for pneumatic conveying systems is high as mining companies require reliable transport solutions for bulk materials like ore, sand, and other minerals. The city also hosts food processing plants that rely on these systems for the bulk transport of ingredients.
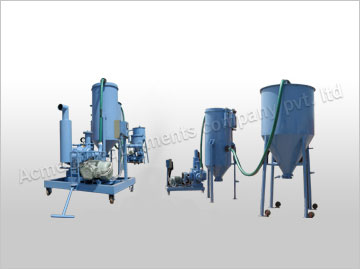
4. Pneumatic Conveying Systems in Curitiba
- Key Industries: Chemicals, food processing, agriculture.
- Reason for Demand: Known for its robust chemical production industry, Curitiba sees a high demand for pneumatic conveying systems. The city’s food processing and agricultural industries also rely on these systems for the movement of grains, powders, and additives.
5. Pneumatic Conveying Systems in Porto Alegre
- Key Industries: Agriculture, food processing.
- Reason for Demand: Porto Alegre is an agricultural hub, and the demand for pneumatic conveying systems is driven by the transportation needs of agricultural products like soybeans and rice. Additionally, the food processing sector in the region uses these systems to transport bulk ingredients efficiently.
Why Is There a Growing Demand for Pneumatic Conveying Systems in Brazil?
- Automation in Industry The Brazilian manufacturing sector is increasingly moving toward automation, and pneumatic conveying systems play a critical role in this transformation. These systems are ideal for automating the transportation of bulk materials across facilities, leading to improved productivity, reduced labor costs, and enhanced operational efficiency.
- Demand for Hygiene and Safety Industries like food processing and pharmaceuticals require strict adherence to hygiene standards. Pneumatic conveying systems help minimize contamination risks by operating in a closed-loop environment, ensuring the safe and hygienic transport of sensitive materials.
- Cost-Effectiveness Pneumatic conveying systems are often more cost-effective than traditional mechanical conveyors, especially in large-scale operations. The reduced need for manual labor, minimized wear and tear, and low maintenance requirements make them a cost-effective solution in Brazil’s industries.
- Versatility and Flexibility Pneumatic conveying systems are highly versatile and can transport a wide range of materials, including powders, granules, chemicals, and agricultural products. This versatility allows industries to handle multiple materials with a single system, reducing the need for specialized equipment and increasing operational efficiency.
- Sustainability With growing concerns about environmental impact and sustainability, pneumatic conveying systems are gaining popularity due to their energy-efficient design. These systems often use compressed air, which can be generated from renewable sources, helping industries reduce their carbon footprint.
Step-by-Step Guide: How Pneumatic Conveying Systems Work
- Material Loading The material to be conveyed is loaded into the system through a feeder or hopper. This feeder ensures a controlled flow of the material into the pneumatic conveying pipeline.
- Air Compression A compressor generates compressed air, which is directed into the pipeline. The air creates a flow that moves the material through the pipeline from one point to another.
- Conveying the Material As the material is pushed through the pipeline by the airflow, it moves along a designated route. Depending on the type of pneumatic conveying system, this can be done via dilute phase (for light materials) or dense phase (for heavier materials) systems.
- Material Discharge The material reaches its destination, where it is separated from the airflow. Filters or separators are used to collect the material while allowing the air to exit the system.
- System Maintenance Regular maintenance is required to ensure the pneumatic conveying system operates efficiently. This includes checking for leaks, inspecting filters, and monitoring air pressure levels to ensure optimal performance.
Conclusion
In conclusion, the demand for pneumatic conveying systems in Brazil is driven by the country’s diverse industries, particularly agriculture, food processing, chemicals, and mining. With growing needs for automation, efficiency, and safety, pneumatic conveying systems are increasingly becoming a critical part of industrial operations in key Brazilian cities. The versatility and cost-effectiveness of these systems ensure that they will continue to be a vital component of Brazil’s industrial growth.
FAQs About Pneumatic Conveying System
The two primary types of pneumatic conveying systems are dilute phase and dense phase. Dilute phase is used for light materials and shorter distances, while dense phase is used for heavier materials and longer distances.
Pneumatic conveying systems are widely used in Brazil’s agricultural, food processing, chemical, and mining industries, where bulk materials like grains, powders, chemicals, and minerals need to be transported.
These systems automate material handling, reducing labor costs and increasing speed and accuracy. They also minimize the need for manual intervention, improving overall efficiency.
Yes, pneumatic conveying systems can be designed to handle hazardous materials safely by incorporating features such as explosion-proof components and enclosed, dust-free environments.
Pneumatic systems offer advantages such as reduced maintenance, versatility in handling a variety of materials, energy efficiency, and a smaller footprint compared to mechanical conveyors.