Table of Contents
Pneumatic conveying systems have become a critical component of industrial material handling in the United States. These systems efficiently transport bulk materials such as powders, granules and fine particles through pipelines using compressed air or gas. The rising demand for automation, safety and efficiency in various industries has significantly increased the adoption of pneumatic conveying technology across multiple sectors.
This article examines the factors driving the demand for pneumatic conveying systems in the U.S., key industries benefiting from their implementation, the geographical distribution of demand and the challenges impacting supply.
Factors Driving the Demand for Pneumatic Conveying Systems
1. Advancements in Industrial Automation
The push towards automated processes has led to a surge in demand for pneumatic conveying systems. Industries such as pharmaceuticals, food processing and plastics are integrating these systems to enhance efficiency, reduce manual handling and improve overall productivity.
2. Stringent Hygiene and Safety Standards
Sectors like food processing and pharmaceuticals require contamination-free material handling. Pneumatic conveying systems provide a fully enclosed transport method, minimizing dust emissions and exposure to hazardous substances, which is essential for compliance with U.S. regulatory standards.
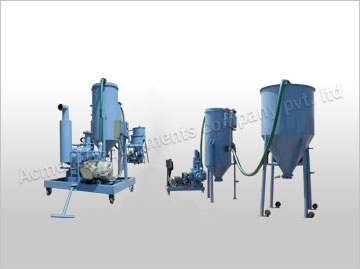
3. Growth in the Chemical and Plastics Sectors
The increasing demand for plastic products and chemical compounds has fueled the need for reliable conveying solutions. Pneumatic systems offer precise material movement, ensuring minimal loss and improved operational efficiency.
4. Expansion of Mining and Heavy Industries
The mining sector benefits from pneumatic conveying systems for transporting fine minerals and ores. These systems offer long-distance material movement, reducing wear and tear on mechanical parts and increasing productivity in mining operations.
Regional Demand for Pneumatic Conveying Systems in the U.S.
The demand for pneumatic conveying systems across the United States is shaped by regional industrial activities, technological advancements, regulatory requirements and economic trends. Each major city has distinct factors influencing its reliance on these systems for bulk material handling and manufacturing efficiency.
New York: Innovation in Pharmaceutical and Food Processing
- Regulatory Influence: New York’s pharmaceutical industry is governed by strict regulations and standards, requiring contamination-free material transfer solutions. Pneumatic conveying ensures precise ingredient handling while maintaining sterility and quality control.
- Technological Advancements: The rise of automation in pharmaceutical and food production has increased the adoption of advanced conveying systems, reducing manual intervention and improving efficiency.
- Economic Impact: The city’s role as a global business hub drives high investment in cutting-edge manufacturing and material handling technologies, making pneumatic conveying a crucial component in industrial operations.
Los Angeles: Enhancing Manufacturing Processes
- Manufacturing Ecosystem: As a major center for automotive, plastics and food packaging industries, Los Angeles relies on pneumatic conveying for precise material transport and waste reduction in production lines.
- Environmental Regulations: The state of California enforces strict air quality and emissions regulations, prompting industries to adopt dust-free, energy-efficient conveying solutions that reduce environmental impact.
- Logistics and Efficiency: Given its status as a major port city, Los Angeles benefits from advanced material handling technologies to streamline logistics in industrial production and packaging.
Chicago: Industrial Growth and Material Handling Challenges
- Infrastructure and Industrial Diversity: Chicago’s well-established industrial infrastructure supports a wide range of manufacturing processes, including chemical processing, pharmaceuticals and heavy industries, all of which require safe and efficient bulk material handling.
- Process Optimization Needs: Pneumatic conveying helps industries address challenges related to product contamination, workplace safety and operational consistency by offering enclosed, automated transport solutions.
- Climate Considerations: The city’s extreme seasonal temperature variations necessitate conveying systems that maintain material integrity and prevent clogging or condensation-related issues in bulk material transport.
Houston: Scaling Up Petrochemical and Energy Operations
- Expansion of Petrochemical Plants: Houston’s status as a leading petrochemical hub creates high demand for large-scale pneumatic conveying systems that can handle powders, catalysts and polymers in refining and processing.
- Workplace Safety and Compliance: The hazardous nature of petrochemical processing necessitates enclosed, dust-free conveying systems to reduce risks associated with combustible materials and airborne contaminants.
- Integration with Energy Sector: Pneumatic conveying systems play a vital role in Houston’s energy industry by efficiently transporting coal, biomass and other raw materials used in power generation and refining.
Detroit: Automation and Efficiency in Automotive and Plastics
- Advancements in Automotive Production: Detroit’s automotive industry is rapidly adopting automation, increasing the need for precise material handling solutions in metal casting, coating applications and component manufacturing.
- Plastics and Composites Growth: As the demand for lightweight vehicle materials grows, plastics and composites manufacturing in Detroit relies on pneumatic conveying for efficient resin and pellet transport.
- Cost-Effective Production Strategies: Pneumatic conveying reduces material waste, increases production speed and enhances workplace safety, making it a preferred solution for Detroit’s high-volume manufacturing plants.
Challenges and Solutions in the Supply of Pneumatic Conveying Systems
The pneumatic conveying industry faces several challenges, including high costs, technical complexities and many more. However, strategic solutions can help mitigate these obstacles and improve system adoption and efficiency.
1. High Initial Investment Costs
Challenge:
- Pneumatic conveying systems require substantial capital investment, making them less accessible to small and mid-sized enterprises.
- The cost of equipment, installation and integration with existing systems can be a financial burden.
Solutions:
- Modular System Design: Offering scalable and modular systems allows businesses to start with a basic setup and expand as needed.
- Flexible Financing Options: Leasing programs and payment plans can help SMEs afford high-quality conveying solutions.
2. Technical Complexity and Maintenance
Challenge:
- Pneumatic conveying systems require specialized expertise for installation, operation and maintenance.
- System blockages, wear and tear and component failures can lead to downtime and increased operational costs.
Solutions:
- Smart Monitoring & Predictive Maintenance: Implementing IoT-based monitoring systems can detect early signs of wear, preventing unexpected breakdowns.
- User-Friendly Designs & Training: Manufacturers should offer intuitive controls and operator training to improve ease of use.
- Comprehensive Maintenance Packages: Service agreements with proactive maintenance can help prevent system failures and ensure longevity.
FAQs on Pneumatic Conveying System
Pneumatic conveying systems are typically categorized into dilute phase and dense phase systems. Dilute phase is suitable for light materials, while dense phase is used for heavier, abrasive materials that need to be transported over long distances.
Pneumatic conveying systems automate the transportation of materials, reducing manual labor and improving production speed. This automation also ensures consistency and minimizes errors.
Regular maintenance includes checking for leaks, cleaning filters, inspecting wear components, and ensuring proper air pressure levels. Routine maintenance helps extend the system’s lifespan and ensures optimal operation.
Yes, pneumatic conveying systems can safely handle hazardous materials when designed with the appropriate safety features, such as explosion-proof components and sealed systems to minimize dust and contamination.
Pneumatic conveying systems provide a hygienic and efficient method of transporting materials, ensuring compliance with regulatory standards for cleanliness and minimizing contamination risks.
In conclusion, pneumatic conveying systems are in high demand in the U.S. due to their efficiency, versatility, and ability to improve safety and hygiene in various industries. The growing need for automation and cost-effective solutions in sectors like food processing, pharmaceuticals, and chemical processing is expected to continue driving demand for these systems across major U.S. cities.