Turbo blowers have emerged as a game-changer for industries that require high-capacity air movement. These highly efficient machines provide significant advantages over traditional blowers by reducing energy consumption, lowering operational costs, and offering better overall performance. Thanks to advancements in technology, turbo blowers are widely used in water and wastewater treatment plants, membrane systems, and various industrial processes.
But what exactly makes turbo blowers so special? Their innovative design, which incorporates high-speed motors, gearless operation, and oil-free lubrication, has been derived from aerospace technology and adapted for industrial use. By understanding the principles behind their operation and the advantages they offer, industries can make informed decisions about incorporating these blowers into their processes.
How Turbo Blowers Work
At the core of turbo blowers is a high-speed rotor, typically powered by a permanent magnet synchronous motor (PMSM) or a variable frequency drive (VFD). Unlike traditional blowers, turbo blowers are gearless, meaning they don’t require the oil or complex gear systems that can wear out over time. Instead, they rely on advanced air or magnetic bearings, which provide frictionless operation and require no lubrication.
This combination of a high-speed rotor and advanced bearings results in a highly efficient air compression system. Turbo blowers operate on the principle of dynamic air movement, where air is drawn into the blower and rapidly compressed by the rotating turbine, resulting in high air pressure and flow rates.
Turbo Blowers
Turbo blowers are designed for specific industrial applications:
- High-Speed Turbo Blowers – These blowers operate at extremely high rotational speeds, making them ideal for applications that require quick air movement, such as filter backwash systems.
- Energy-Efficient Turbo Blowers – Designed to minimize energy consumption, these blowers are perfect for industries aiming to reduce their environmental impact and lower energy costs.
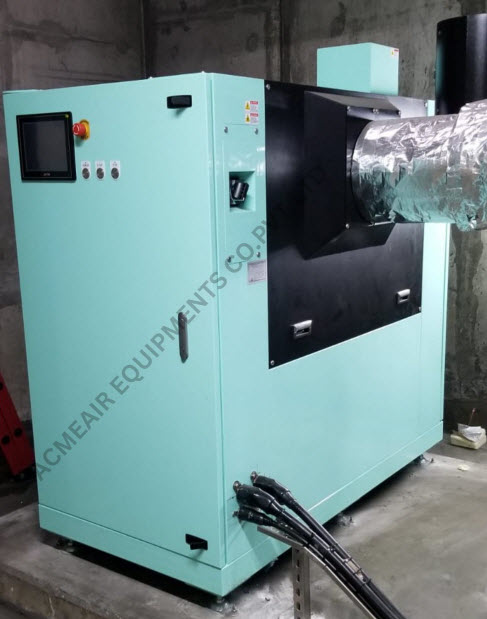
Key Features of Modern Turbo Blowers
Modern turbo blowers offer a range of advanced features that set them apart from traditional blowers. Some of the key features include:
- Gearless Design: The absence of gears reduces mechanical losses and increases the blower’s lifespan.
- Oil-Free Operation: Thanks to air or magnetic bearings, turbo blowers don’t require oil for lubrication, making them more environmentally friendly and reducing maintenance needs.
- Smart Functionality: Turbo blowers are increasingly being integrated with Industry 4.0 practices, allowing for remote monitoring, programmable start/stop functions, and real-time diagnostics.
- Noise Reduction: Many turbo blowers come with dust-tight air-cooled sound enclosures that significantly reduce noise levels, ensuring quieter operation in industrial environments.
Energy Efficiency of Turbo Blowers
Energy efficiency is one of the most significant benefits of turbo blowers. Traditional blowers often operate with inefficient mechanical systems that waste energy through heat and friction. In contrast, turbo blowers use high-speed rotors and frictionless bearings to compress air with minimal energy loss.
This efficiency can lead to substantial cost savings. Industries that switch to turbo blowers often see a significant reduction in their electricity consumption, which not only lowers operational expenses but also contributes to a reduced carbon footprint.
Applications of Turbo Blowers
Turbo blowers are used in a wide range of industrial applications, including:
- Water and Wastewater Treatment: Turbo blowers play a crucial role in aeration systems, ensuring that oxygen is effectively distributed throughout the water to support biological treatment processes.
- Membrane Applications: In industries where membrane filtration is used, turbo blowers help maintain the required air pressure and flow for efficient filtration.
- Filter Backwash Systems: Turbo blowers are ideal for applications that require frequent start and stop operations, such as backwashing filters to remove accumulated particles.
Advancements in Turbo Blower Technology
Recent advancements in turbo blower technology have significantly improved their functionality and reliability. For instance, many modern turbo blowers now feature:
- Remote Monitoring: Operators can monitor and control blowers remotely, improving convenience and reducing the need for on-site supervision.
- Advanced Safety Features: Turbo blowers are equipped with safety mechanisms such as automatic shutdown in case of malfunction, helping to protect the equipment and personnel.
- Dust-Tight Enclosures: These enclosures protect the blower from contaminants while also reducing noise levels, making turbo blowers suitable for more environments.
High-Speed Turbo Blowers: Key Advantages
High-speed turbo blowers offer unparalleled performance when it comes to rapid air movement. Their ability to operate at extremely high speeds makes them particularly valuable for time-sensitive processes, such as wastewater treatment, where consistent air flow is essential for effective biological processing.
Energy-Efficient Turbo Blowers: A Closer Look
Energy-efficient turbo blowers are engineered to minimize energy consumption without sacrificing performance. By using advanced bearings and high-efficiency motors, these blowers can deliver the same level of air pressure and flow as traditional blowers, but with far less energy usage. This makes them a popular choice for industries focused on sustainability and cost reduction.
Selecting the Right Turbo Blower for Your Needs
When choosing a turbo blower, it’s essential to consider factors such as the required air flow, the blower’s power capacity, and the specific needs of your industrial process. Additionally, it’s important to work with a reputable turbo blower manufacturer that can provide after-sales support and spare parts to ensure the blower operates reliably over time.
Turbo Blower Maintenance and Longevity
One of the key advantages of turbo blowers is their low maintenance requirements. The absence of gears and the use of oil-free bearings mean that there are fewer mechanical components to wear out. Regular inspections and timely replacement of worn parts can extend the life of a turbo blower significantly.
Challenges in the Turbo Blower Industry
While turbo blowers offer numerous advantages, they also present some challenges. For instance, overcoming industry hesitance to adopt new technologies can be difficult. Additionally, some turbo blowers can produce vibrations that may affect nearby machinery or processes, though modern designs have addressed many of these concerns.
Future Trends in Turbo Blowers
As industries continue to prioritize energy efficiency and sustainability, the demand for turbo blowers is expected to rise. Future developments in smart monitoring and automation will likely make these blowers even more attractive, allowing for greater control and optimization of industrial processes.
Conclusion
Turbo blowers represent a significant leap forward in blower technology, offering unmatched efficiency, durability, and performance. Whether you’re looking to reduce energy costs or enhance the reliability of your air compression systems, turbo blowers provide a robust solution for a wide range of industrial applications. With continued advancements in technology, the future of turbo blowers looks even brighter.
FAQs – Turbo Blowers
Turbo blowers are commonly used in industries like water and wastewater treatment, chemical processing, and food and beverage production.
Turbo blowers save energy by using high-efficiency motors, gearless designs, and frictionless bearings, which reduce mechanical losses.
With proper maintenance, turbo blowers can last for many years, often outlasting traditional blowers due to their lower mechanical wear and tear.
Yes, many modern turbo blowers come equipped with remote monitoring features, allowing operators to control and diagnose issues from a distance.
Turbo blowers are designed with sound-dampening enclosures to minimize noise, making them quieter than many traditional blower systems.