Mechanical vacuum boosters are essential components in vacuum systems, known for their ability to enhance performance, increase efficiency and handle demanding industrial applications. Their unique design and operational capabilities make them indispensable in sectors like oil distillation, degassing, coating and semiconductor processing. This article delves into the working principle of mechanical vacuum boosters and highlights how they optimize vacuum systems for various industries.
What is a Mechanical Vacuum Booster?
A mechanical vacuum booster is a type of vacuum pump designed to increase the performance of primary vacuum pumps. It works by creating a pressure differential that enhances the efficiency and capacity of the vacuum system.
Mechanical vacuum boosters are highly effective in applications where a deep vacuum is required, such as distillation, coating and refining processes.
Key Components of Mechanical Vacuum Boosters
Design and Construction:
Mechanical vacuum boosters consist of two counter-rotating impellers with a special contour. These impellers rotate without physical contact, maintaining precise and sharp clearances for efficient operation.
Twin or Tri-Lobe Configurations:
Depending on the application, vacuum boosters can be designed with twin or tri-lobe impellers. Twin lobe designs offer simpler construction, while tri-lobe designs enhance efficiency and reduce noise levels.
Cooling Mechanisms:
These boosters are available in air-cooled and water-cooled variants to suit different operating environments and temperature requirements.
High Efficiency:
Designed to handle vapours and gases at lower specific power consumption, they ensure constant and precise volume displacement, making them energy-efficient.
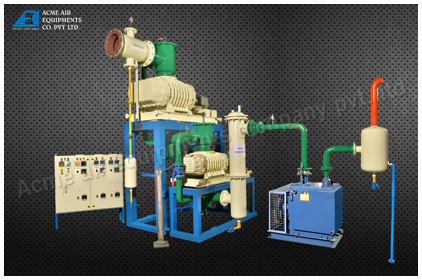
Working Principle of Mechanical Vacuum Boosters
The operation of mechanical vacuum boosters relies on the synchronized rotation of the impellers, which compress and transport gases or vapours through the system. Here’s a step-by-step explanation:
Compression Without Physical Contact:
The impellers in the booster rotate in opposite directions within a finely machined housing. They do not come into contact with each other or the casing, minimizing wear and tear while ensuring long operational life.
Pressure Differential Creation:
The rotating impellers create a pressure differential that draws gases or vapours from the primary vacuum pump. This pressure differential boosts the performance of the overall vacuum system.
Precise Volume Displacement:
The design of the impellers allows for consistent and precise volume displacement, ensuring stable operation even under varying loads.
Low Power Consumption:
The boosters are engineered to handle large volumes of gases and vapours at lower specific power consumption, making them cost-effective and energy-efficient.
Handling of Vapours and Gases:
Mechanical vacuum boosters are designed to efficiently process gases and vapours, which are common in industrial applications like oil refining and coating.
Benefits of Mechanical Vacuum Boosters
Enhanced Vacuum System Efficiency:
By increasing the overall capacity and efficiency of the vacuum system, mechanical vacuum boosters enable faster processing and better performance.
Energy Savings:
The low power consumption of vacuum boosters reduces operational costs, making them an economical choice for industries.
Durable and Reliable Design:
The absence of physical contact between the impellers and the casing minimizes wear, ensuring a longer operational lifespan and reduced maintenance requirements.
Adaptability to Various Applications:
The ability to handle diverse gases and vapours makes vacuum boosters suitable for a wide range of industrial processes.
Precise Operation:
The constant volume displacement provided by the impellers ensures stable and reliable vacuum levels, even under demanding conditions.
Applications of Mechanical Vacuum Boosters
Mechanical vacuum boosters are used across a variety of industries due to their versatility and efficiency. Below are some of their most common applications:
Oil Distillation and Refining
Vacuum boosters play a crucial role in re-used oil distillation processes, where they create the deep vacuum required for separating and purifying oil products. Their precise operation ensures efficient separation at lower energy costs.
Degassing
In industries like metallurgy and polymer production, degassing is essential to remove trapped gases from molten metals or plastics. Mechanical vacuum boosters enhance the efficiency of degassing processes by creating a consistent vacuum environment.
Coating Processes
Vacuum boosters are widely used in the coating industry for processes such as thin-film deposition and metallization. Their ability to maintain stable vacuum levels ensures high-quality and uniform coatings.
Semiconductor Processing
The semiconductor industry relies on vacuum systems for etching, doping and deposition processes. Mechanical vacuum boosters help achieve the precise vacuum conditions required for these delicate operations.
Vacuum Impregnation
In industries like automotive and electronics, vacuum impregnation is used to seal porous materials. Vacuum boosters ensure thorough penetration of sealing agents, enhancing the durability and reliability of components.
Space Simulation
Vacuum boosters are essential in creating space-like conditions for testing aerospace components. Their ability to handle large volumes of gases at low pressures makes them ideal for this application.
Freeze Drying
In the pharmaceutical and food industries, freeze drying is used to preserve products by removing moisture under vacuum. Mechanical vacuum boosters improve the efficiency and speed of the freeze-drying process.
Factors to Consider When Selecting a Mechanical Vacuum Booster
Choosing the right vacuum booster for your application involves evaluating several factors:
Capacity Requirements:
The volume of gases or vapours to be handled should match the booster’s capacity for optimal performance.
Cooling Type:
Select between air-cooled or water-cooled configurations based on the operational environment and cooling needs.
Material of Construction:
Ensure the booster is made from materials compatible with the gases or vapours being processed to prevent corrosion or wear.
Application-Specific Features:
Consider features like twin or tri-lobe designs for enhanced efficiency and noise reduction.
Technological Advancements in Mechanical Vacuum Boosters
Modern vacuum boosters incorporate cutting-edge technology to meet the demands of advanced industrial processes:
- Improved Rotor Designs:
Advanced rotor designs enhance efficiency and reduce noise levels, meeting stringent industry standards. - Compact and Modular Designs:
Space-saving designs make it easier to integrate vacuum boosters into existing systems. - Environmental Compliance:
Enhanced designs reduce emissions and ensure compliance with environmental regulations.
Impact of Mechanical Vacuum Boosters on Industrial Processes
Mechanical vacuum boosters significantly enhance the performance of vacuum systems, leading to:
- Reduced Operational Costs: Lower energy consumption and maintenance requirements.
- Higher Product Quality: Precise vacuum conditions ensure better end-product quality.
- Scalability: Modular designs allow for easy scaling of vacuum systems to meet growing production needs.
FAQs About Mechanical Vacuum Boosters
Mechanical vacuum boosters enhance vacuum systems by increasing efficiency and capacity. They are used in oil distillation, degassing, coating and semiconductor processing.
They operate using counter-rotating impellers that create a pressure differential, drawing gases or vapours from the primary pump and boosting system performance.
Twin lobes are simpler and cost-effective, while tri-lobe designs offer higher efficiency, reduced noise and improved performance in demanding applications.
Industries such as oil refining, pharmaceuticals, food processing, aerospace and electronics benefit significantly from vacuum boosters.
Capacity, cooling type, material compatibility, efficiency and application-specific features are key considerations when choosing a vacuum booster.
Conclusion
Mechanical vacuum boosters are indispensable for modern industrial processes requiring efficient and reliable vacuum systems. Their advanced design, energy efficiency and adaptability to various applications make them a valuable investment for industries ranging from oil refining to semiconductor manufacturing. With technological advancements and a focus on sustainability, mechanical vacuum boosters are set to remain a cornerstone of industrial innovation.